■补充与整理:耀德讲堂/ 邱耀弘博士
※红字为Dr. Q补充之说明,大陆端原作者不可考。
技术补充说明
- 半固态在大陆被称之为触变(Thixo),意指材料金属材料在接近熔点附近产生碰触会变成液体,但不碰触则为固体的特殊现象,此现象被翻译为触变(碰触改变相态),如图1所示。

- 此技术主流是在日本,主要流行期间在2000~2010十年间,当时的笔记本电脑与翻盖按键手机,但镁合金的表面处理一直没有办法很理想地展现镁金属的光泽(轻但易氧化),逐渐地淡出市场。
- 镁合金大约比重可以分布在3~1.7g(最轻的是镁锂合金),在未来的新能源电动车或许又会重新被提出讨论。
摘要
本文对半固态射出成型镁合金AZ91D的组织与性能进行了分析,如表1所表示为AZ91D的化学成分表与机械性能的要求标准。结果表明,该成型法所生产的镁合金产品的组织及力学性能均优于压铸产品,从而为应用半固态射出成型法进行镁合金汽车零部件的生产奠定基础。

引言
近年来,随着对绿色、环保等方面的要求逐渐提高,镁合金以其重量轻、比强度高、比刚度高、减震性好、耐电磁遮罩、易回收等特点从众多金属材料中脱颖而出,广泛的应用于航空、航太、电子和汽车等行业。目前,镁合金应用的两大热点产业是电子业和汽车业。一方面,用于“3C”(Computer, Communication, Consumption Electronics Products) 产品的壳体,有逐渐取代可回收性较差的塑胶壳体之趋势;另一方面,作为实际应用中最轻的结构金属,镁合金能够满足交通运输业日益严格的节能和尾气排放要求,从而生产出重量轻、耗油少、环保的新一代交通工具。
各国广泛采用的镁合金成型方法为压铸法。压铸镁合金产品具有尺寸稳定性好、生产率高等优点,但也具有夹杂多、气孔多、成型后难热处理、尺寸近净成型差等不足。采用压铸法制造的零件很难满足诸如用于“3C”产品中所广泛使用的薄壁壳体类零件以及用于汽车工业中的高性能镁合金零部件的要求。
同压铸法相比,半固态方法制造的产品具有铸造缺陷少、产品的力学性能、尺寸精度、表面和内在品质高等优点。此外,还有节约能源、安全性好、近净成型性好等优点。目前世界上已经成功工业化的镁合金半固态成型技术是半固态射出成型技术[1]。台湾公司的汉达电脑(佛山)、富士镁合金(昆山)、大陆的华禹镁业有限公司(长春)是大陆境内最早引进此项技术的厂家,采用均势以本文利用华禹镁业的半固态射出成型机制备试样,对半固态射出成型镁合金的组织及力学性能进行了分析,从而为公司下一步进行汽车用高性能镁合金的研究开发作适当的技术储备。
- 不过半固态射出镁合金仍旧有技术上必须注意的地方,由于耐高温要求必须使用DC55(SKD11改性),模具热损耗高且射出机为专用机,所有耐高温紧固件都是比原来塑胶射出成型用(~350℃)的高出一倍以上之耐温要求。另外由于射出后毛边、螺丝孔、减肉厚处都必须倚赖CNC加工,还有镁合金是双相金属,酸和碱都能与其反应,射出的镁合金坯如果不即时处理导致受潮,会容易有白点锈蚀。
另外有关材料的回收部份,由于镁合金的活性高,半固态射出法必须使用切成片条状(四方形断面长条2X2X5~8mm),射出后流道(水口)料无法如压铸法直接熔融回收,镁合金无法像铝合金可以在无保护状态下熔融,这是使用此门工艺必须要事先理解的。 - 此外,二次加工铝合金和镁合金的风险在于金属尘暴、活性金属废弃品堆积造成起火的风险,在大陆昆山有多次的案例,镁合金半固态射出与铝合金压铸有相同的风险,一定要注意在射出、压铸、铸件打磨与后处理过程必须格外谨慎。
半固态射出成型技术的原理及工艺过程
半固态射出成型技术的原理
在普通铸造过程中,初晶以枝晶方式长大,当固相率达到0.2左右时,枝晶就形成连续网路骨架,失去宏观流动性。半固态成型是在液态金属从液相到固相冷却过程中进行强烈搅拌,使普通铸造成型时易于形成的树枝晶网路骨架被打碎而保留分散的颗粒状组织形态,悬浮于剩余液相中。这种颗粒状非枝晶的显微组织,在固相率达0.5~0.6时仍具有一定的流变性,从而可利用常规的成型工艺如压铸、挤压、模锻等实现金属的成型。
半固态射出成型法是近些年来开发的一种新工艺,源于美国DOW化学公司,美国THIXOMAT公司将其商业化。该工艺是将塑胶的射出成型原理与半固态金属成型工艺相结合,集半固态金属浆料的制备、输送、成型等过程于一体,该法较好地解决了半固态金属浆料的保存输送、成型控制困难等问题。
半固态射出成型技术的工艺过程
射出成型法主要工艺过程如下:被制成颗粒的镁合金原料(由枝状晶镁合金铸锭制成,其组织仍为枝状晶组织)从料斗中加入;在套筒中的镁合金原料通过电加热转变成半固体状态,在螺杆的剪切作用下,在套筒中半固体金属浆料形成了近乎于球形状的固体颗粒,在射出缸的作用下,以相当于塑胶射出机的十倍速率压射到模具内成型。半固态(大陆称之为触变)射出成型机的基本结构如图2所示。

试验设备及方法
半固态射出成型试样的制备
本文采用日本制钢所(Japan Steel Work, JSW)的半固态射出成型机制备了标准力学性能试样,在不同制备条件下,考察了目前最广泛使用的镁合金AZ91D (9%Al+1%Zn的镁合金)组织与性能的变化以及耐腐蚀性能。该成型机的外观如图3所示,试样模具由日本制钢所提供,所制备的测试试样如图4所示,成型过程中模具温度为180℃。射出完毕时不需要喷冷却剂来降低模具的表面温度,与传统的压铸机不同,因此设备周围非常洁净。

- 由于温度很高的镁合金射出料没有办法设计热流道,因此JSW开发长喷嘴(Long Nozzle)技术,加长的射出喷嘴深入模穴附近,因此模具的强度受到考验。
图4中由左至右依次为标准冲击试样、标准蠕变试样、标准拉伸试样与硬度试样,在论文只采用标准拉伸试样进行试验,分别考察不同工艺条件下,半固态镁合金组织与性能的变化。

快速腐蚀条件如下:腐蚀介质为0.5% NaCl或0.1mol NaCl溶液;试验温度:室温(静态)或35±1℃;腐蚀测试时间:120小时(因为镁合金活性高,要求测试的时间很长)。
- AZ91D属于铸造镁合金类,主要依靠压力模具铸造辅以后加工的方式加工,可以用电泳等表面方式改变外观。特点是比强度高且耐腐蚀较纯镁大幅提高,主要用于电器产品的壳体、小尺寸薄型或异型支架等。A代表金属铝Al,Z代表金属锌Zn,9代表铝的含量为9%,1代表锌的含量为1%,最后的D为辨识代码。
结果与讨论
半固态射出成型镁合金的组织分析
图5中组织是取自不同工艺参数制备标准拉伸试棒的中部,其工艺参数的区别主要表现在料筒温度的差别,在图5中由工艺(a)至工艺(d)料筒温度逐步升高。

由图5可见,在不同工艺参数条件下,半固态镁合金组织的变化不大,主要差别表现在缺陷的数量和大小方面(金属熔融状态的蒸发造成气孔缺陷,尤其在高速高压射出下的气旋通常会卷入肉厚变化较大的区域)。可见,料筒温度对半固态镁合金成型性具有决定性的影响,在料筒温度较低的条件下,半固态浆料的流变性不足,成型性能不足,提高料筒温度可以明显的提高半固态浆料的流变性能,但会明显降低固相率,在工艺d的条件下,除晶粒细小外,其组织已经接近普通压铸合金组织。因此,在实际产品制备中必须控制好料筒温度和组织这两方面的因素,才有可能获得高品质的产品。
图6为半固态镁合金组织的扫描电镜照片。由图6a可见,半固态镁合金试棒的组织细小、均匀,图6b为放大的晶界相,对晶界相的定点能谱分析表明,其晶界相的主要组成为Mg和Al,并含有少量的Zn。

根据图6表示地定点能谱分析结果如图7所示。对半固态镁合金进行线扫描的结果表明Al和Zn主要分布在晶界上,在晶内分布较少,Mg则主要分布在晶内,在晶界处Mg含量明显减少,如图8所示。以上结果表明半固态射出成型镁合金的组织形态及分布基本与压铸组织相同。


半固态射出成型AZ91D的力学性能分析
- 半固态射出成型AZ91D的力学性能
图9中示出了50根试棒(图4工艺d条件下)中随机抽取5根试棒的力-位移曲线、力-变形曲线以及力学性能的测量资料。由此可见,半固态射出成型试棒已达到了很高的强度,其平均断裂强度可达到270MPa以上,平均屈服强度可达150MPa左右,由于镁合金试棒在拉伸过程中没有明显的屈服点,故而以σp0.2(0.2的应力变形)估算其屈服强度。 - 盐水快速腐蚀对于半固态射出成型AZ91D性能的影响
镁合金的抗腐蚀性能是衡量镁合金性能的一个重要指标,本文采用快速腐蚀试验考察了经快速腐蚀后半固态成型镁合金试棒组织与性能的变化。所采用试棒与前述力学性能试棒相同。图10展示出了经120小时快速腐蚀后AZ91D镁合金试棒的力学性能。可见,腐蚀后镁合金试棒力学性能明显下降,平均断裂强度下降到220MP左右,屈服强度下降至120MPa左右。腐蚀试验结果表明,尽管半固态组织细小、致密,但其抗腐蚀性能仍相当差,做为重要结构部件和装饰性壳体类零部件时,仍须采用适当的表面处理工艺,否则将无法满足使用要求。


结论
近年来,世界各国高度重视镁合金的研究与开发,将镁资源作为21世纪的重要战略物资,加强了镁合金在汽车、电脑、通讯及航空航太领域的应用开发研究。美、日、欧等发达国家目前已经投入大量人力和物力,实施多项大型联合研究发展计画,研究汽车用镁合金零部件,这些研究开发计画加快了国外应用镁合金零部件的步伐。中国是一个摩托车生产、消费大国和出口大国,也是一个潜在的汽车生产和消费大国。然而,目前中国的镁合金成型技术还相对落后,镁合金零部件的力学性能及耐腐蚀性能较低是制约汽车用镁合金零部件在中国应用的一个重要因素。
本文通过对半固态射出成型AZ91D镁合金试棒的显微组织、力学性能分析和快速腐蚀试验,得出如下结论:
- 应用半固态射出成型技术可得到组织细小、致密,力学性能相对较高的镁合金部件。
- 其综合力学性能优于目前被广泛采用的压铸镁合金部件。
- 半固态射出成型设备的费用高昂,以及必须支付专利许可的费用,加之成型用原材料-镁粒的成本较高,整体投资比较大。因而该技术尤其适用于那些具有较高要求和高附加值的产品。
- AZ91D是否能够使用NMT技术(Nano Molding Technology, 奈米成型技术)与一种材料的工程塑胶进行结合?没有资料显示可行性,目前仍有待三井化学的资料(当时极度保密)。不过已经得知普通镁合金AZ31是可以采用NMT技术的。
原文网址:https://www.smartmolding.com/22-04c02/
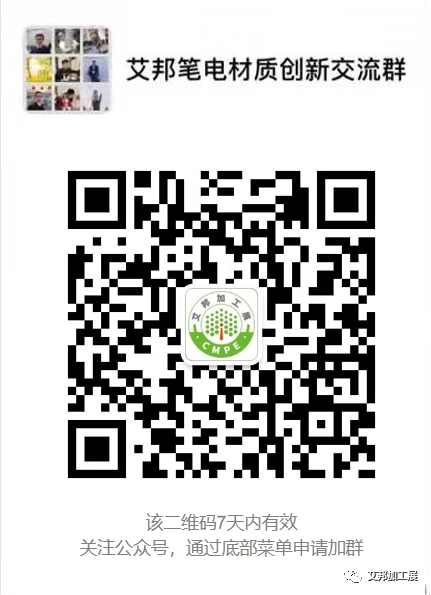
微信扫描下方的二维码阅读本文