镁合金是目前工程应用中重量轻的工程金属材料,具有比重轻、导热性好、电磁屏蔽能力强、易于回收等特点,被认为是21世纪富于开发和应用潜力的“绿色材料”,目前已在汽车电子、航天、通讯等行业得到了应用。
一、镁合金材料优点
1、重量轻
镁合金作为一种轻质金属结构材料,其密度为铝的2/3、钢的1/4;在同等刚性条件下,1Kg镁合金的坚固度等于18Kg铝和2.1Kg钢,这一特性对于现代手提类产品的重量减轻及车辆能耗减少有重要意义。
2、吸震性能高
镁有极好的滞弹吸震性能,可吸收震动与噪音。在相同载荷下,其减振性是铝的100倍、钛合金的300~500倍,抗冲击性是塑料的20倍。用于设备机壳可减少噪音传递、提高防冲击与防凹陷能力。
3、切削性能良好
镁有良好的切削性能,能接受较高的切削速度,可减少切削加工时间,延长刀具使用寿命;有优良的表面光洁度,并可一次切削获得,极少出现积屑瘤;有良好的断屑特性及温度传导性,可免于使用冷却液或润滑液。
4、再生性
废旧镁合金铸件可再熔化作为AZ91D、AM50或AM60的二次材料进行铸造。由于压铸件的需求不断增长,可回收的能力是非常重要的,也更符合环保要求。
二、镁合金材料在笔电中的应用
笔记本电脑(以15寸笔电为例)常用镁合金与铝合金的对比:
目前在轻量化要求下,轻薄笔电结构件产品主厚都在0.5~0.6mm,传统压铸工艺已不能满足要求,因此笔电镁合金薄壁件加工主要采用半固态射出成型,及少量的冲压成型。
下面我们来了解一下,镁合金成型技术。
三、镁合金的成型技术
根据成型工艺的不同,镁合金材料主要分为铸造镁合金和变形镁合金两大类。前者主要通过铸造获得镁合金产品。包括砂型铸造、永久型铸造、熔模铸造、消失模铸造、压铸等。其中压铸是最成熟、应用最广的技术,目前90%以上的镁合金产品是压铸成形的。。而后者则是通过变形生产尺寸多样的板、棒、管、型材及锻件产品。并且可以通过材料组织的控制和热处理工艺的应用,获得更高的强度、更好的延展性、更好的力学性能,从而满足更多结构件的需要。另外,镁合金的半固态成型作为一种新型铸造技术也得到了广泛的研究与应用。
目前采用较多的镁合金成型方法和主要工艺如下表所示:
成型方法 |
主要工艺 |
优点 |
缺点 |
液态成型 |
压铸法 |
产品尺寸稳定、生产率高 |
夹杂和气孔多、成型后难热处理、尺寸净成型差,不适用薄壁壳体零件类加工 |
半固态成型 |
触变注射成型 |
铸造缺陷少,产品的力学性能、尺寸精度、表面和内在质量高 |
技术复杂、对设备要求高 |
塑性成型 |
轧制、热挤压、冲压 |
变形镁合金的二次成型,对技术和设备的要求不高 |
无法进行镁合金的二次塑性深加工 |
四、铸造镁合金成型技术介绍
压铸是镁合金最主要、应用最广泛的成形工艺。用镁合金可以很容易地生产壁厚1.0mm~2.0mm的压铸件,现在最小壁厚可达0.6mm。镁压铸件的铸造斜度为1.5,而铝合金是2~3度。镁压铸件的尺寸精度比铝压铸件高50%。镁合金的熔点和结晶潜热都低于铝合金,压铸过程中对模具冲蚀比铝合金小,且不易粘型,其模具寿命可比铝合金件长2—4倍。镁合金件压铸周期比铝件短,因而生产效率可比铝合金提高25%。镁合金铸件的加工性能优于铝合金铸件,镁合金件的切削速度可比铝合金件提高50%,加工耗能比铝合金件低50%。生产经验表明由于生产效率高,热室压铸的镁合金小件的总成本低于冷室压铸的铝合金同样件。
压铸镁合金可按其成分分为四个系列:AZ系列(AZ91)、AM系列(AM60、AM50)、AS系列(AS41、AS21)、AE系列(AEA2)。
镁合金压铸时,合金液冲填压型时的高速湍流运动,使腔内气体无法排出,会导致组织疏松,甚至铸件表面鼓包或变形。压铸工艺参数如压力、速度、熔体温度、模具温度等对铸件性能都有显着影响。许多新压铸方法,包括真空压铸、充氧压铸和挤压铸造等一定程度上克服了以上缺点,减少了铸件组织疏松和气孔等缺陷,提高了铸件致密度。
另外,1)熔模铸造是目前国际上较为先进的铸造技术之一,熔模铸造从原理上讲适合于制备小体积高精密的铸件,目前它已用于生产铝合金甚至镍基超合金。2)消失模铸造是一种近无余量、精确成型的新型铸造技术,镁合金的消失模铸造具有较巨大的应用前景。
五、变形镁合金成型技术介绍
变形镁合金不同于铸造镁合金的液态成形,而是通过在300℃—500℃温度范围内挤压、轧制、锻造的方法固态成形。由于变形加工消除了铸造组织缺陷及细化了晶粒,故与铸造镁合金相比,变形镁合金具有更高的强度、更好的延展性和更好的力学性能,同时生产成本更低。
目前镁合金的塑性成形过程主要为锻造和挤压,少量为轧制成形,且均需采用热加工方式。因此,变形温度是重要参数,同时变形速率和应力状态也是重要的考虑因素。
1)锻压成形:镁合金锻造性能取决于3个因素:合金的凝固温度、变形速率及晶粒大小。为了保证良好的加工性能必须采用具有可锻性的AZ和ZK系镁合金坯料或坯棒。这两系合金可通过添加晶粒细化剂和合金元素得到满意的晶粒尺寸。但铸造组织的晶粒度一般不符合锻造要求,须先将铸锭加以挤压,得到锻造所需晶粒尺寸,再以高变速率锻造成形。镁合金在其固相线温度以下55℃范围内进行锻造,锻造温度过低可能形成裂纹。液压机和低速机械压力机是其模锻的常用设备。
2)挤压成形:镁合金可以挤压成各种管材、棒材和型材。包括带凹角和暗槽的型材,大直径和变截面厚度的薄壁管等难加工的产品。挤压材料也是AZ和ZK系镁合金,温度一般控制在300℃—460℃之间,具体温度的选择还和特定的合金牌号和挤压形状有关。因为镁在变形过程中会产生大量热,所以挤压过程中必须充分冷却,否则合金温度可能超过固相线温度而导致开裂。
3)轧制成形:铸造成平面形状且有圆形边缘的镁锭可以用来进行厚板和薄板的轧制。一般镁合金厚板厚度范围为11.0mm—70mm,薄板厚度为0.8mm—10mm。镁合金的冷轧性能不佳,一般厚板可以在热轧机上直接生产,而薄板一般采用冷轧和温轧两种方式生产。
超塑性变形
另外,超塑性是指晶体材料在拉伸时表现出大的应变。金属及合金在一定条件下的流变应力应变速率敏感性指数m大于0.3,表现出特大伸长率(200%~3000%)的性能称为超塑性。镁合金的室温变形能力低,但是在超塑性状态下却有很高的塑性,可利用超塑性加工形状复杂的零件与模锻件。
超塑性加工镁合金产品的主要有以下优点:
1、成品率高:成品率可达90%以上,且产品表面缺陷少,可减少后续工序与生产成本。例如,日本用不同方法生产镁合金笔记本电脑外壳,压铸法的成品率在70%左右,而超塑性成形法的可达91%。
2、产品厚度薄:用超塑性工艺生产的产品,厚度比压铸件及半固态压铸件产品要薄很多。例如用超塑冲压锻造生产的镁合金工件其厚度可达0.4mm,而压铸件及半固态压铸件的大多在0.8mm以上。
3、形状复杂、变形量大的工件可一次成型,并具有流动性高,填充性好、加工设备工作推力小等特点。
4、产品成形时不产生弹性变形,成形后几乎不会发生回弹,工件尺寸精确,表面粗糙度也小。
镁合金超塑性成型在提出伊始就引起了很多企业的关注,一些具备条件的企业已经开始着手相关设备的研发并成功试样。估计再过不久,待设备和技术都成熟了,镁合金超塑性产品会在多个行业发挥重要作用。
六、镁合金半固态射出成型技术介绍
成型原理:在室温条件下,颗粒状的镁合金原料由料斗强制输送到料筒中,料筒中旋转的螺杆使合金颗粒向模具运动,当其通过料筒的加热部位时,合金颗粒呈现半固态,在螺旋体剪切作用下,呈半固体的枝晶组织的合金转变成颗粒状初生相组织,当累计到预定体积时,以高速5m/s将其压入到预热模具中成型,目前广泛应用于笔电外观件。
工艺流程:半固态射出成型由塑胶射出成型衍生应用在金属的成型制程,其工艺流程:喷涂脱模剂→合模→射出→成型→取出成型件。根据工艺流程的不同,半固态成形通常分为流变铸造(Rheocasting)和触变铸造(Thixocasting)两类:流变铸造是对冷却过程中的金属液进行搅动,将形成的固相枝晶破碎,形成一定固相分数的半固态金属浆料,然后将浆料注入压铸机或挤压机内成形(俗称“一步法”);而触变铸造是先由连铸等方法制得具有半固态金属组织的锭坯,然后切成所需长度,用二次加热装置再加热到半固态状态,最后移送至压铸机等再压铸或挤压成形(俗称“两步法”)。
工艺优势:笔电外壳采用半固态射出成型产品具有组织均匀,无缩孔缩松缺陷等优势,其综合力学性能与锻件相近,高于传统压铸件,通过半固态成型技术增加强镁铝合金等轻合金的力学性能。
与压铸比较,半固态射出成型有如下优势:
七、存在的问题及前景展望
近年来,镁合金应用逐年提高,但一些尚待解决的问题使得镁合金的广泛生产受到限制。表现在以下几个方面:镁的化学活性很强,在空气中易氧化,在高温情况下可以发生燃烧,因此熔炼过程中须采用复杂的保护措施。工业中主要采用熔剂保护法和气体保护法。熔剂保护法最大缺点是反应过程中产生的有害气体严重污染环境并损害人体健康;而气体保护法中经常采用且具有良好保护效果的SF6气体,但其温室效应是CO2的23500倍;镁常温下成形性差,目前工业上应用的多为镁合金压铸件,限制了其它成形方法的运用;镁合金没有像铝合金那样大规模使用的另一个原因是其耐蚀性差,采用表面防护又增加了其生产成本。
鉴于以上问题,镁合金研究集中在以下几个方面:无污染熔炼技术;开发和改善镁合金的成形工艺;进一步研究镁合金的表面处理技术,改善其外观和耐蚀性以及高强韧镁合金和耐热镁合金的研究。
文章来源:镁途
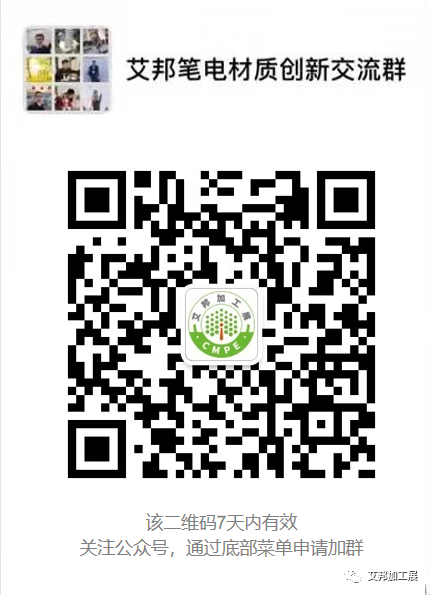
2022-09-15
2023-06-25
2023-04-19
2023-02-06
第五届笔记本电脑材质创新高峰论坛 9月21日 重庆富力假日酒店
(重庆市沙坪坝区高新区大学城南路26号)
论坛议题(包括但不限于):
|
|
|
|
|
|
|
|
|
|
|
|
|
|
|
|
|
|
|
|
|
|
|
|
|
|
|
|
|
|
|
|
|
|
|
|
|
|
|
|
|
|
|
|
|
|
|
|
|
|
|
|
|
|
|
|
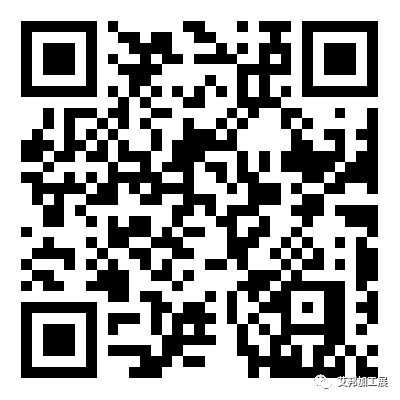
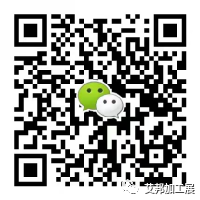

!
原文始发于微信公众号(艾邦加工展):镁合金成型技术介绍
微信扫描下方的二维码阅读本文